Механички заптивкииграат многу важна улога во избегнувањето на истекувањето за многу различни индустрии. Во поморската индустрија постојатмеханички заптивки за пумпа, механички заптивки на ротирачки вратило. И во нафтената и гасната индустрија имамеханички заптивки со кертриџ,разделени механички заптивки или механички заптивки на сув гас. Во автомобилската индустрија постојат водни механички заптивки. А во хемиската индустрија постојат мешачки механички заптивки (механички заптивки за мешање) и компресорски механички заптивки.
Во зависност од различните услови на употреба, потребно е механичко заптивање со различен материјал. Постојат многу видови материјали што се користат вомеханички заптивки на вратило како што се керамички механички заптивки, јаглеродни механички заптивки, силиконски карбидни механички заптивки,SSIC механички заптивки иTC механички заптивки.
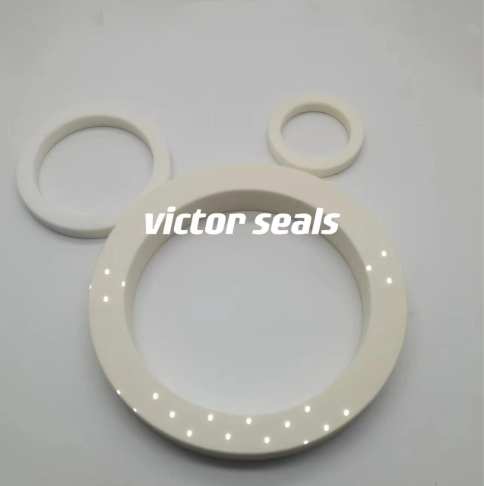
Керамички механички заптивки
Керамичките механички заптивки се критични компоненти во различни индустриски апликации, дизајнирани да спречат истекување на течности помеѓу две површини, како што се ротирачко вратило и стационарно куќиште. Овие заптивки се високо ценети поради нивната исклучителна отпорност на абење, отпорност на корозија и способност да издржат екстремни температури.
Примарната улога на керамичките механички заптивки е да го одржат интегритетот на опремата со спречување на губење на течности или контаминација. Тие се користат во бројни индустрии, вклучувајќи нафта и гас, хемиска преработка, третман на вода, фармацевтска индустрија и преработка на храна. Широката употреба на овие заптивки може да се припише на нивната издржлива конструкција; тие се направени од напредни керамички материјали кои нудат супериорни перформанси во споредба со другите материјали за заптивки.
Керамичките механички заптивки се состојат од две главни компоненти: едната е механичка стационарна површина (обично изработена од керамички материјал), а другата е механичка ротирачка површина (обично изработена од јаглероден графит). Дејството на заптивање се случува кога двете површини се притиснати заедно со сила на пружина, создавајќи ефикасна бариера против истекување на течности. Додека опремата работи, подмачкувачкиот филм помеѓу површините за заптивање го намалува триењето и абењето, додека одржува цврсто заптивање.
Еден клучен фактор што ги разликува керамичките механички заптивки од другите видови е нивната извонредна отпорност на абење. Керамичките материјали поседуваат одлични својства на тврдост што им овозможуваат да издржат абразивни услови без значително оштетување. Ова резултира со подолготрајни заптивки кои бараат поретка замена или одржување од оние направени од помеки материјали.
Покрај отпорноста на абење, керамиката покажува и исклучителна термичка стабилност. Тие можат да издржат високи температури без да претрпат деградација или губење на ефикасноста на запечатување. Ова ги прави погодни за употреба во апликации со високи температури каде што другите материјали за запечатување може предвреме да откажат.
Конечно, керамичките механички заптивки нудат одлична хемиска компатибилност, со отпорност на разни корозивни супстанции. Ова ги прави привлечен избор за индустриите кои рутински работат со груби хемикалии и агресивни течности.
Керамичките механички заптивки се неопходнизаптивки на компонентидизајнирани да спречат истекување на течности во индустриска опрема. Нивните уникатни својства, како што се отпорноста на абење, термичката стабилност и хемиската компатибилност, ги прават префериран избор за различни апликации во повеќе индустрии.
керамички физички својства | ||||
Технички параметар | единица | 95% | 99% | 99,50% |
Густина | г/см3 | 3.7 | 3,88 | 3.9 |
Тврдост | ХРА | 85 | 88 | 90 |
Стапка на порозност | % | 0,4 | 0,2 | 0,15 |
Јачина на фрактура | МПа | 250 | 310 | 350 |
Коефициент на топлинска експанзија | 10(-6)/К | 5,5 | 5.3 | 5.2 |
Топлинска спроводливост | З/МК | 27,8 | 26,7 | 26 |
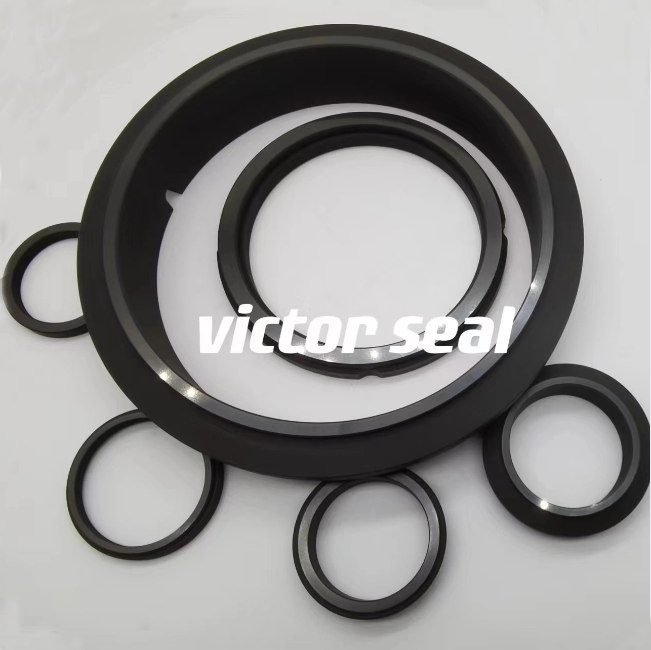
Јаглеродни механички заптивки
Механичкото јаглеродно заптивка има долга историја. Графитот е изоформа на елементот јаглерод. Во 1971 година, Соединетите Американски Држави го проучувале успешниот флексибилен графитен материјал за механичко заптивка, кој го решил проблемот со истекување на атомскиот енергетски вентил. По длабинска обработка, флексибилниот графит станува одличен материјал за заптивка, од кој се прават разни јаглеродни механички заптивки со ефект на заптивка на компоненти. Овие јаглеродни механички заптивки се користат во хемиската, нафтената, електричната енергија, како што се заптивките за флуиди на висока температура.
Бидејќи флексибилниот графит се формира со експанзија на експандиран графит по висока температура, количината на интеркалациски агенс што останува во флексибилниот графит е многу мала, но не целосно, па затоа постоењето и составот на интеркалацискиот агенс имаат големо влијание врз квалитетот и перформансите на производот.
Избор на материјал за предна површина на заптивката од јаглерод
Оригиналниот пронаоѓач користел концентрирана сулфурна киселина како оксиданс и средство за интеркалација. Меѓутоа, откако била нанесена на заптивката на метална компонента, откриено е дека мала количина сулфур што останува во флексибилниот графит го кородира контактниот метал по долготрајна употреба. Со оглед на оваа точка, некои домашни научници се обиделе да го подобрат, како што е Сонг Кемин, кој избрал оцетна киселина и органска киселина наместо сулфурна киселина. Оцетна киселина, бавна во азотна киселина и намалена температура на собна температура, направена од мешавина од азотна киселина и оцетна киселина. Со користење на мешавина од азотна киселина и оцетна киселина како средство за вметнување, бил подготвен експандиран графит без сулфур со калиум перманганат како оксиданс, а оцетната киселина полека се додавала во азотната киселина. Температурата се намалува на собна температура и се прави мешавина од азотна киселина и оцетна киселина. Потоа во оваа смеса се додаваат природниот графит во снегулки и калиум перманганат. Под постојано мешање, температурата е 30°C. По реакција од 40 минути, водата се мие до неутрална состојба и се суши на 50~60°C, а експандираниот графит се прави по експанзија на висока температура. Овој метод не постигнува вулканизација под услов производот да достигне одреден волумен на експанзија, со цел да се постигне релативно стабилна природа на материјалот за заптивање.
Тип | M106H | M120H | M106K | M120K | M106F | M120F | M106D | М120Д | M254D |
Бренд | Импрегниран | Импрегниран | Импрегниран фенол | Антимон јаглерод (А) | |||||
Густина | 1,75 | 1.7 | 1,75 | 1.7 | 1,75 | 1.7 | 2.3 | 2.3 | 2.3 |
Јачина на фрактура | 65 | 60 | 67 | 62 | 60 | 55 | 65 | 60 | 55 |
Компресивна цврстина | 200 | 180 | 200 | 180 | 200 | 180 | 220 | 220 | 210 |
Тврдост | 85 | 80 | 90 | 85 | 85 | 80 | 90 | 90 | 65 |
Порозност | <1 | <1 | <1 | <1 | <1 | <1 | <1,5 | <1,5 | <1,5 |
Температури | 250 | 250 | 250 | 250 | 250 | 250 | 400 | 400 | 450 |
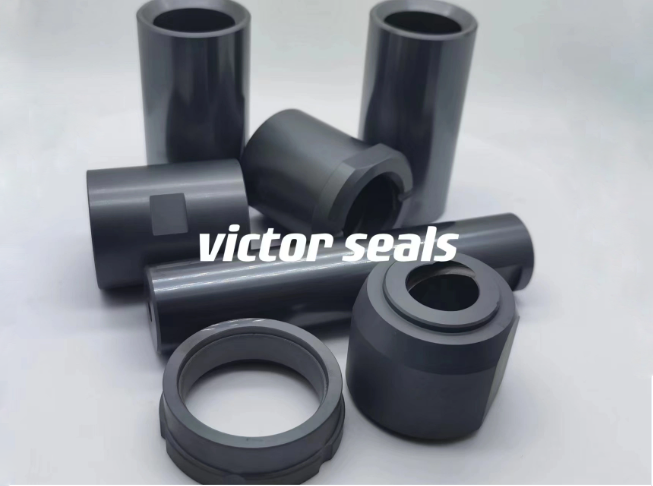
Силициум карбидни механички заптивки
Силициум карбидот (SiC) е исто така познат како карборунд, кој е направен од кварцен песок, нафтен кокс (или јагленов кокс), дрвени струготини (кои треба да се додадат при производство на зелен силициум карбид) и така натаму. Силициум карбидот, исто така, има редок минерал по природа, дудинка. Во современите C, N, B и други неоксидни високотехнолошки огноотпорни суровини, силициум карбидот е еден од најшироко користените и најекономични материјали, кој може да се нарече златен челичен песок или огноотпорен песок. Во моментов, индустриското производство на силициум карбид во Кина е поделено на црн силициум карбид и зелен силициум карбид, кои се хексагонални кристали со сооднос од 3,20 ~ 3,25 и микротврдост од 2840 ~ 3320 kg/m².
Производите од силициум карбид се класифицираат во многу видови според различната околина на примена. Генерално се користат повеќе механички. На пример, силициум карбидот е идеален материјал за механичка заптивка од силициум карбид поради неговата добра отпорност на хемиска корозија, висока цврстина, висока тврдост, добра отпорност на абење, мал коефициент на триење и отпорност на високи температури.
SIC заптивните прстени можат да се поделат на статички прстени, подвижни прстени, рамни прстени и така натаму. SiC силициум може да се направи во разни карбидни производи, како што се ротирачки прстени од силициум карбид, стационарно седиште од силициум карбид, силициум карбидна чаура и така натаму, во зависност од посебните барања на клиентите. Може да се користи и во комбинација со графитен материјал, а неговиот коефициент на триење е помал од алуминиумската керамика и цврстите легури, па затоа може да се користи во висока PV вредност, особено во услови на силна киселина и силна алкалија.
Намаленото триење на SIC е една од клучните придобивки од неговата употреба во механичките заптивки. Затоа, SIC може да издржи абење подобро од другите материјали, продолжувајќи го животниот век на заптивката. Дополнително, намаленото триење на SIC ја намалува потребата од подмачкување. Недостатокот на подмачкување ја намалува можноста за контаминација и корозија, подобрувајќи ја ефикасноста и сигурноста.
SIC исто така има одлична отпорност на абење. Ова укажува дека може да издржи континуирана употреба без да се оштети или скрши. Ова го прави совршен материјал за употреба што бара високо ниво на сигурност и издржливост.
Исто така, може повторно да се лакира и полира, така што заптивката може да се обнови повеќе пати во текот на својот век на траење. Генерално се користи повеќе механички, како на пример кај механичките заптивки поради неговата добра отпорност на хемиска корозија, висока цврстина, висока тврдост, добра отпорност на абење, мал коефициент на триење и отпорност на високи температури.
Кога се користи за површини на механички заптивки, силициум карбидот резултира со подобрени перформанси, зголемен век на траење на заптивките, пониски трошоци за одржување и пониски трошоци за работа на ротирачка опрема како што се турбини, компресори и центрифугални пумпи. Силициум карбидот може да има различни својства во зависност од тоа како е произведен. Реакционо врзан силициум карбид се формира со поврзување на честички од силициум карбид едни со други во реакционен процес.
Овој процес не влијае значително врз повеќето физички и термички својства на материјалот, но сепак ја ограничува хемиската отпорност на материјалот. Најчестите хемикалии што претставуваат проблем се каустиците (и други хемикалии со висока pH вредност) и силните киселини, и затоа силициум карбидот врзан со реакција не треба да се користи со овие апликации.
Реакција-синтерирана инфилтриранасилициум карбид. Во таков материјал, порите на оригиналниот SIC материјал се пополнуваат во процесот на инфилтрација со согорување на металниот силициум, со што се појавува секундарен SiC и материјалот стекнува исклучителни механички својства, станувајќи отпорен на абење. Поради неговото минимално собирање, може да се користи во производство на големи и сложени делови со тесни толеранции. Сепак, содржината на силициум ја ограничува максималната работна температура на 1.350 °C, а хемиската отпорност е исто така ограничена на околу pH 10. Материјалот не се препорачува за употреба во агресивни алкални средини.
СинтеруваноСилициум карбид се добива со синтерување на претходно компресиран многу фин SIC гранулат на температура од 2000 °C за да се формираат силни врски помеѓу зрната на материјалот.
Прво, решетката се згуснува, потоа порозноста се намалува, а на крај врските меѓу зрната се синтеруваат. Во процесот на таква обработка, се јавува значително намалување на производот - за околу 20%.
SSIC заптивка е отпорен на сите хемикалии. Бидејќи во неговата структура не е присутен метален силициум, може да се користи на температури до 1600C без да се влијае на неговата цврстина.
својства | R-SiC | S-SiC |
Порозност (%) | ≤0,3 | ≤0,2 |
Густина (g/cm3) | 3.05 | 3.1~3.15 |
Тврдост | 110~125 (HS) | 2800 (кг/мм2) |
Модул на еластичност (Gpa) | ≥400 | ≥410 |
Содржина на SiC (%) | ≥85% | ≥99% |
Содржина на Si (%) | ≤15% | 0,10% |
Јачина на свиткување (Mpa) | ≥350 | 450 |
Цврстина на притисок (кг/мм2) | ≥2200 | 3900 |
Коефициент на топлинска експанзија (1/℃) | 4,5×10-6 | 4,3×10-6 |
Отпорност на топлина (во атмосферата) (℃) | 1300 | 1600 |
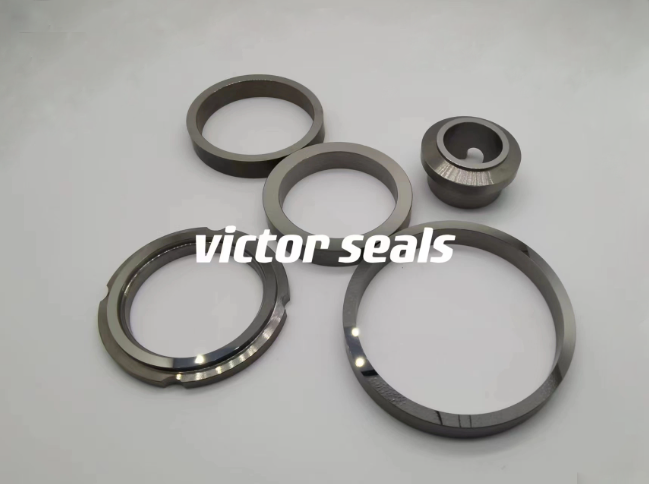
TC механичка заптивка
ТК материјалите имаат карактеристики на висока тврдост, цврстина, отпорност на абење и отпорност на корозија. Познат е како „Индустриски заб“. Поради своите супериорни перформанси, широко се користи во воената индустрија, воздухопловството, машинската обработка, металургијата, дупчењето на нафта, електронската комуникација, архитектурата и други области. На пример, во пумпи, компресори и мешалки, прстените од волфрам карбид се користат како механички заптивки. Добрата отпорност на абење и високата тврдост го прават погоден за производство на делови отпорни на абење со висока температура, триење и корозија.
Според неговиот хемиски состав и карактеристиките на употреба, TC може да се подели во четири категории: волфрам-кобалт (YG), волфрам-титаниум (YT), волфрам-титаниум тантал (YW) и титаниум-карбид (YN).
Тврдата легура од волфрам кобалт (YG) е составена од WC и Co. Погодна е за обработка на кршливи материјали како што се леано железо, обоени метали и неметални материјали.
Стелитот (YT) е составен од WC, TiC и Co. Поради додавањето на TiC во легурата, неговата отпорност на абење е подобрена, но цврстината на свиткување, перформансите на мелење и топлинската спроводливост се намалени. Поради неговата кршливост при ниски температури, погоден е само за брзо сечење општи материјали, а не за обработка на кршливи материјали.
Волфрам титаниум тантал (ниобиум) кобалт (YW) се додава во легурата за да се зголеми тврдоста на високи температури, цврстината и отпорноста на абење преку соодветна количина на тантал карбид или ниобиум карбид. Во исто време, цврстината се подобрува и со подобри перформанси на сеопфатно сечење. Главно се користи за сечење на тврди материјали и повремено сечење.
Базната класа на карбонизиран титаниум (YN) е тврда легура со тврда фаза од TiC, никел и молибден. Нејзините предности се висока тврдост, способност против сврзување, антиабење против полумесечина и способност против оксидација. На температура над 1000 степени, сè уште може да се обработува машински. Применлива е за континуирано доработка на легиран челик и челик за калење.
модел | содржина на никел (тежински%) | густина (g/cm²) | тврдост (HRA) | цврстина на свиткување (≥N/mm²) |
YN6 | 5.7-6.2 | 14,5-14,9 | 88,5-91,0 | 1800 година |
YN8 | 7.7-8.2 | 14,4-14,8 | 87,5-90,0 | 2000 година |
модел | содржина на кобалт (тежински%) | густина (g/cm²) | тврдост (HRA) | цврстина на свиткување (≥N/mm²) |
YG6 | 5.8-6.2 | 14,6-15,0 | 89,5-91,0 | 1800 година |
YG8 | 7,8-8,2 | 14,5-14,9 | 88,0-90,5 | 1980 година |
YG12 | 11.7-12.2 | 13.9-14.5 | 87,5-89,5 | 2400 |
YG15 | 14.6-15.2 | 13.9-14.2 | 87,5-89,0 | 2480 |
YG20 | 19.6-20.2 | 13.4-13.7 | 85,5-88,0 | 2650 |
YG25 | 24,5-25,2 | 12.9-13.2 | 84,5-87,5 | 2850 |